Noise Testing Software
GN-1100 series
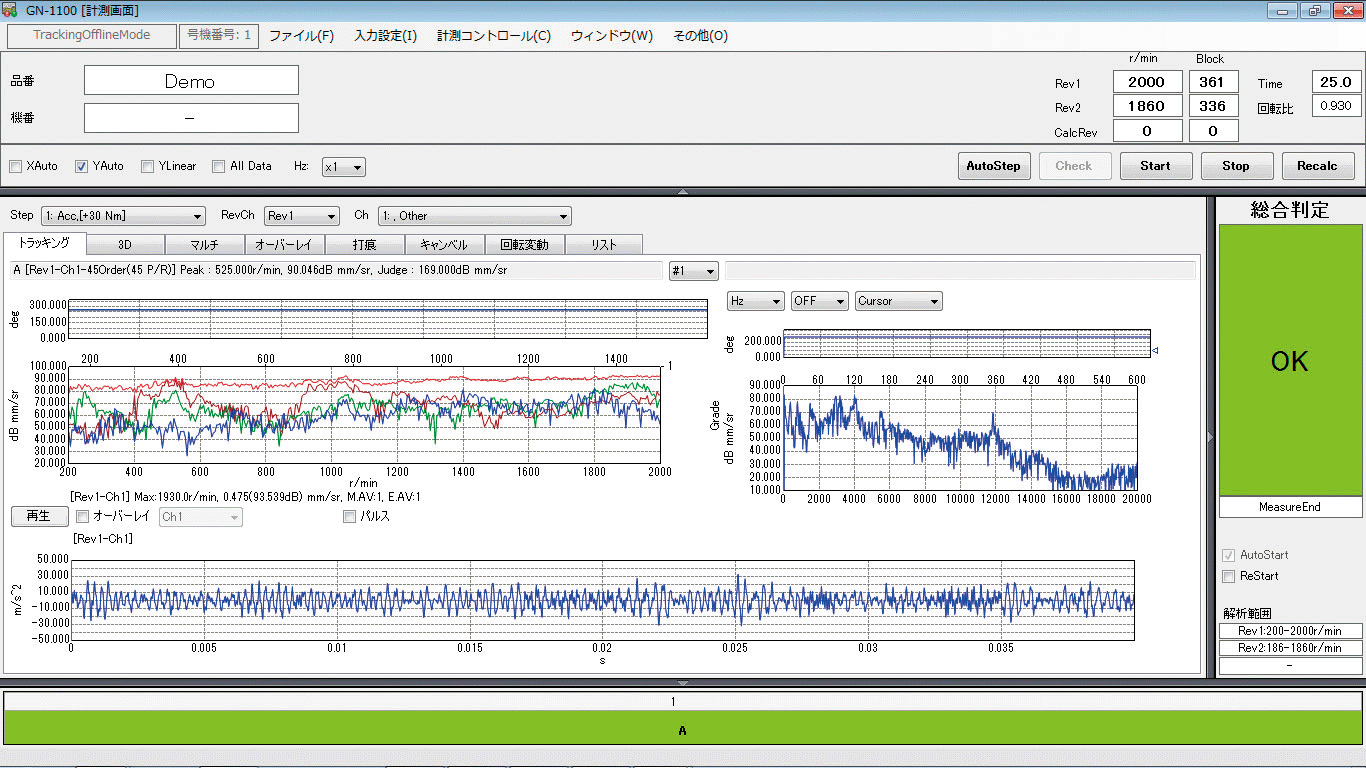
This software has a comparator function for abnormality diagnosis based on sound/vibration analysis.
You can perform simultaneously the tracking analysis and pass/fail judgment for 2 revolution input channels.
It is ideal for vibration analysis of CVT and in-line 100% inspection such as carrier noise analysis of motors.
Features
Major windows
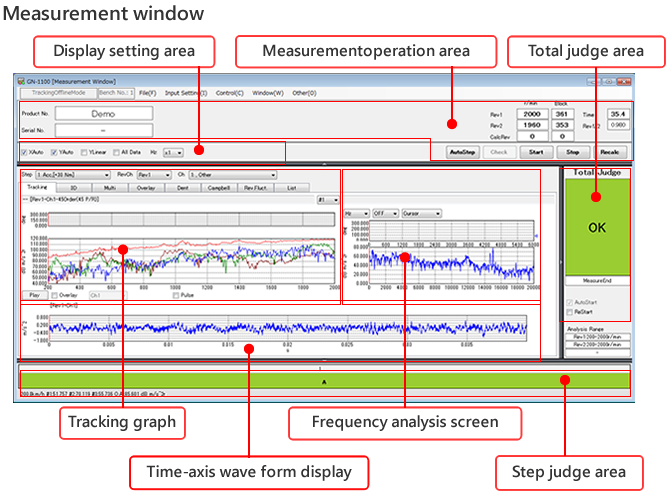
Pattern setting
Up to 20 steps of measurement patterns can be selected by combinations of three items (acceleration/deceleration/constant speed).
Upper/lower-limit rotation speeds and data import interval can be set to each step of each input (Rev1, Rev 2 and calculation revolution).
Noise judgment
Judgment, displaying on the screen, and signal output
1. Sections of judge line:up to 32
2. Judge line setting:up to 32
3. Multi judge function
Function (Option)
Able to read and recalculate the ORF (ONO SOKKI original format of time-series data) format data.
In addition to the recalculation function, following functions are available.
It is effective to improve the measurement by checking resonance and abnormal movement of the work piece.
When the offline tracking mode is connected to the DS-3200 series hardware,
reanalysis is possible by changing the analysis condition immediately after measurement using the most recently recorded data.
Also, reanalysis of the ORF file imported to the following read-only screen is possible in the selected analysis condition.
* GN-0100 is only available for reading and recalculation of ORF file.
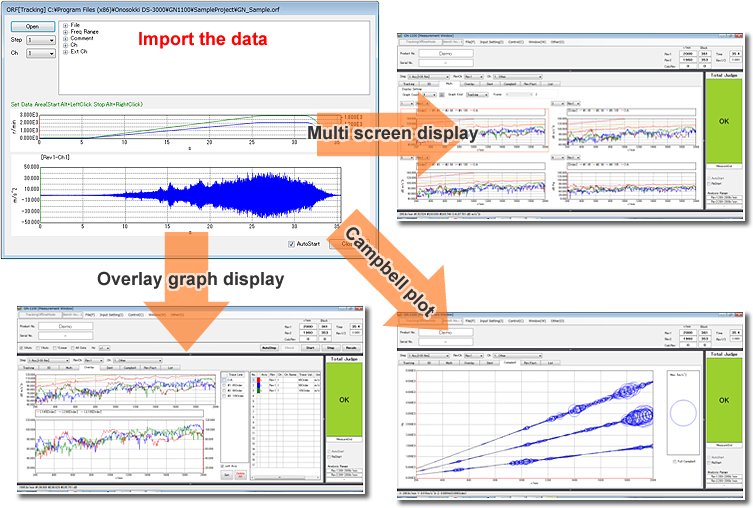
Rotating fluctuation analysis display
Useful for abnormality diagnosis of bearing or gear dents. Characteristic natural frequency peaks seen when they are damaged can be checked
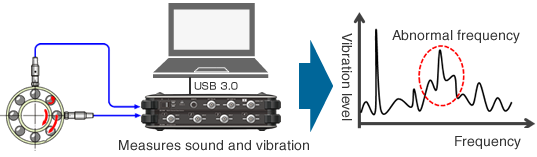
Judgment by Partial Overall
The peak becomes large when a bearing or a gear has damage. The damage can be checked by narrowing to specific frequency bands and making judgments using power addition.
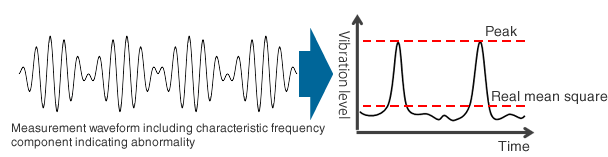
Judgment by Crest factor
Focusing on that the measurement waveform has the characteristic frequency component when damaged, the breakage can be checked by making judgment with peak value/real mean square.
The measurement data and pass-fail judgment of workpiece of the sound/vibration devices can be outputted when the GN-1100 is connected to the device which performs the test of workpiece in the transmission or engine production line. The communication formats are LAN, RS-232C*, DIO*, etc.
* Special order products.
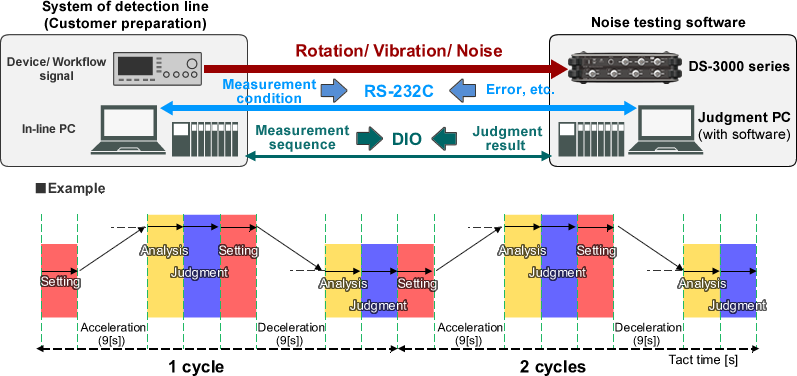
This function is for data management of the large number of files which has been measured and made judgment by the GN-1100. It can be used for searching the workflow information of measured data, and enables to narrow down the multiple workflow data measured in similar condition to perform overlay comparison or averaging.
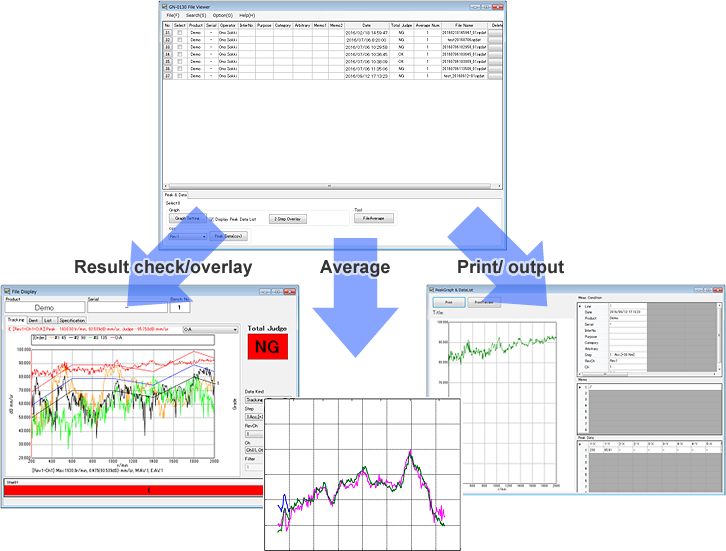
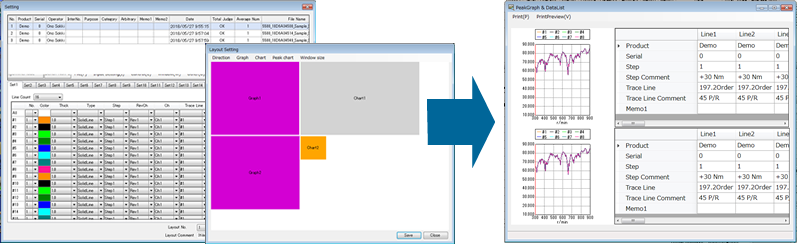
This function is for the simultaneous tracking measurement which is standardized the Rev 1/ Rev 2/ calculation revolution in each step.
Calculation revolution can be set by combination of four arithmetic operation buttons, based on Rev1 and Rev2.
To use this function, it is possible to perform tracking analysis which is based on the rotating input
and output axes with no correlation or rotating axis which cannot be perform rotating measurement for more detailed workflow checking.
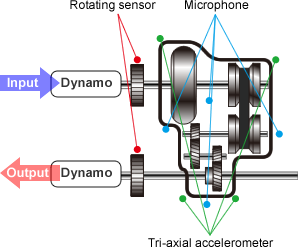
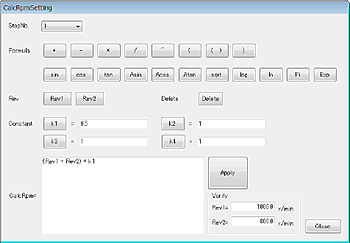
With the GN-0230, envelope processing is applied to the time-axis waveforms of the measured vibration and sound pressure,
and the magnitude at peak, the phase (period), the ratio for each period of the waveform are monitored.
It is suitable for detecting abnormalities that occur in a specific period.
The GN-0160 is effective for checking the presence of dents on gears and scratches on bearings.
It can be used for the measurement during not only constant rotation speed but also acceleration/deceleration.
1. Dent measurement:Up to 32 pairs
2. Number of rotation axis:Up to 6 axes
3. Reference rotation:Rev1/Rev2
4. Rotation ratio:Rotation speed ratio/gear ratio
* When using the envelope analysis function, the peak value is used for each rotation.
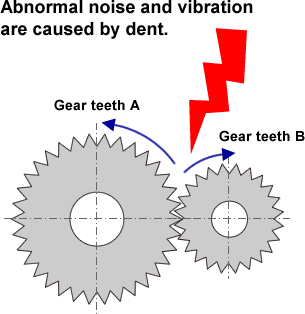
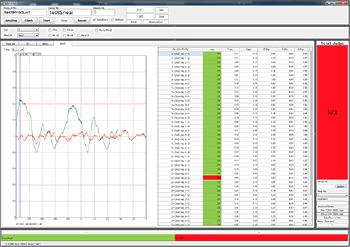
The GN-0170 can make pass/fail judgment of work and equipment by 1/3 octave analysis. This function makes it possible to quantitatively perform "judgment close to the auditory sensation of human" having a characteristic proportional to the frequency component, and supports to build up the human-independent test system.
Also, it can recalculate the optimum threshold using data group judged to be normal in the past, and automatically generate judgment lines.
This function contributes to reduce man-hours in standard management at the time of judgment.
Setting example of judgment line
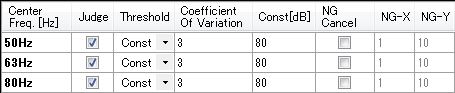
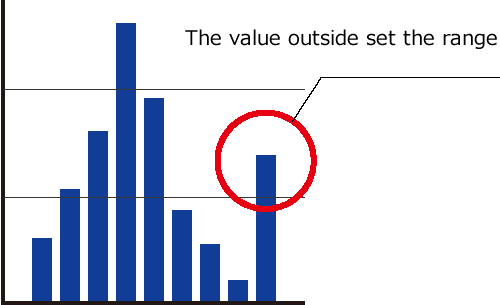
Statistically processes normality judgment data and automatically generates judgment lines. The value outside the normality range is judged to be abnormal.
* Manual setting is also possible (file import etc.).
Application example
Abnormality inspection of transmission and speed reducer
Abnormality inspection of a motor
Abnormality inspection of an engine
Analysis of low frequency sound
Measurement of equipment noise/ vibration
Measurement of sound pressure characteristics of various acoustic products
You can specify the series of operational commands from setting change to result output, and call them later to perform the same operation repeatedly.
Describing commands promotes efficiency of recalculations, and reduces operation errors.
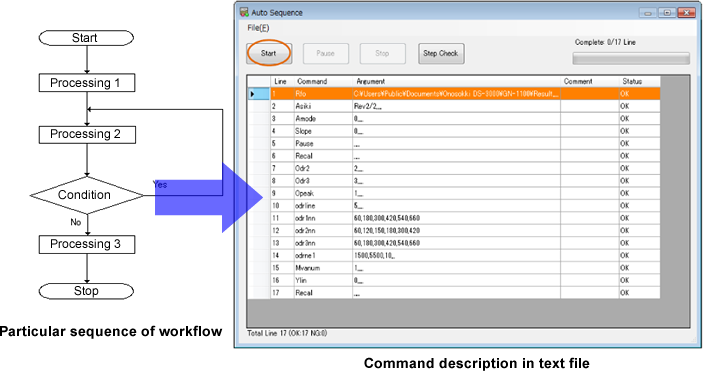
This function allows tracking analysis of the noise caused by the carrier frequency, which is used to change the frequency driving a gear from an inverter in hybrid automobiles, and the order originated from the carrier frequency.
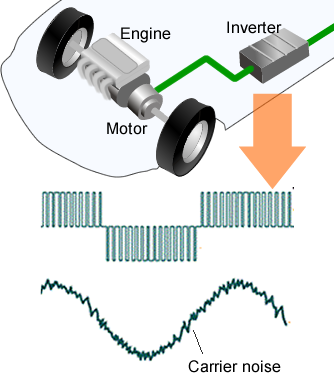
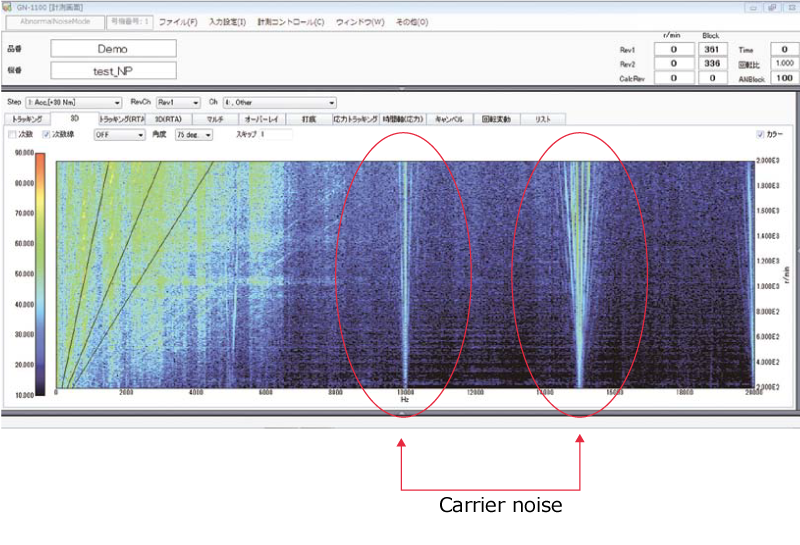
In grade line function, grade line is created as the base for comparing and assessing a work by the measured peak values of sound/ vibration in different measurement facilities.
To manage the multiple measurement data in the specification information setting, any specification information can be attached to the measurement data.
This function can be used for mass production workflow grade guideline or data management in the quality control division. It will be able to use for visualizing of the dispersion or quality difference of workflow.
This function analyzes in real time the repeated stress and load behaviors applied when the works are in operation by using detected signal of a strain gauge. Helpful to check the strength and safety.
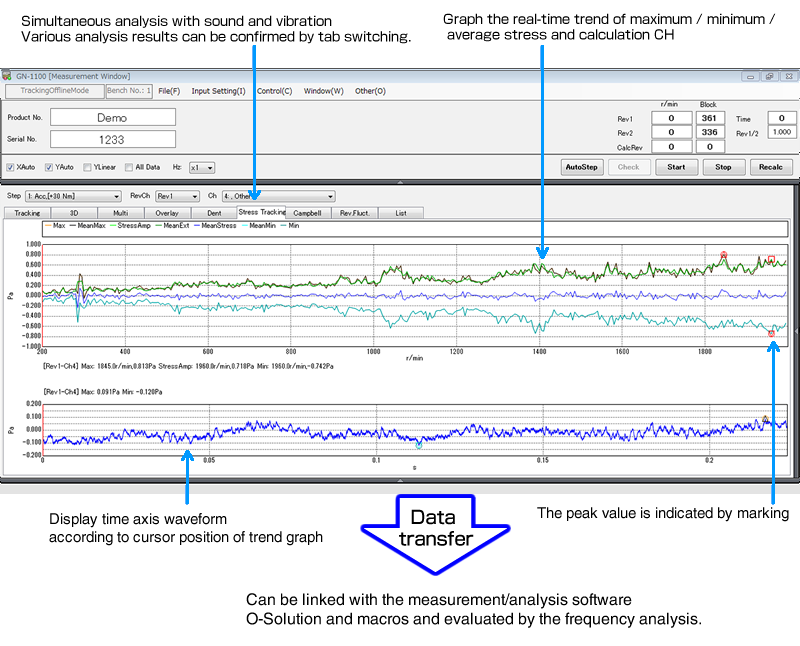
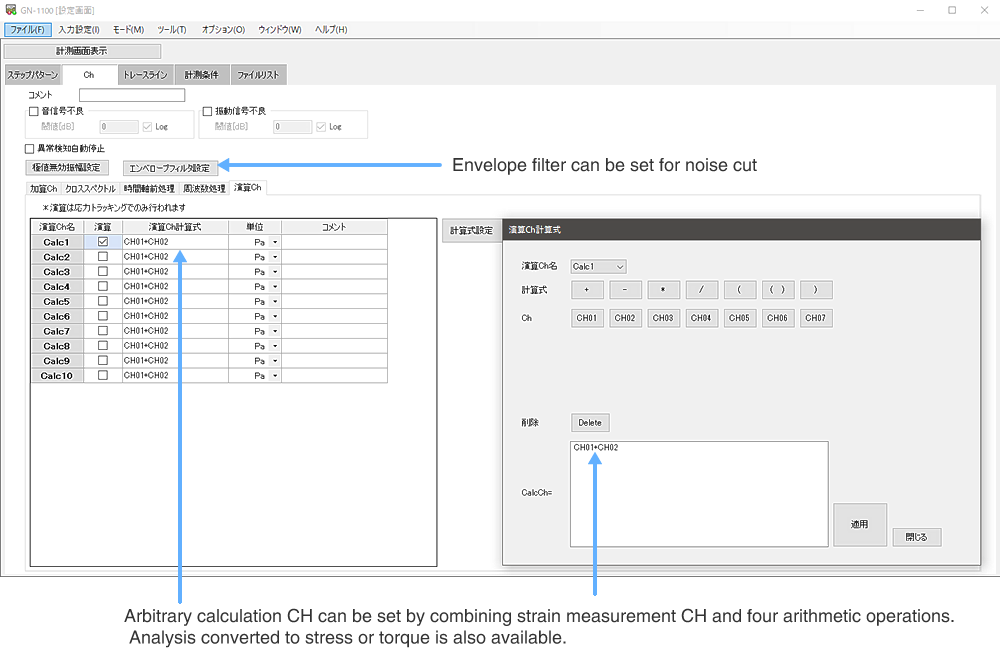
Application example
Production line quality inspection of unit, such as motor, transmission, and speed reducer.
Abnormality inspection of prototype vehicles and parts incorporated in test equipment.
Strength evaluation of new materials.
And other various scenes
This function calculates the difference in rotation speed between the rotation speed signal from the reference axis
and the compared axis, and outputs the torsional amount of the rotating shaft.
If a high load or high torque is applied to a part or unit in the direction of rotation, it may cause abnormalities such as shaft damage
or abnormal noise. By using this function, it is possible to evaluate the torsional amount and obtain data for verifying the durability
of parts and the presence or absence of abnormalities.
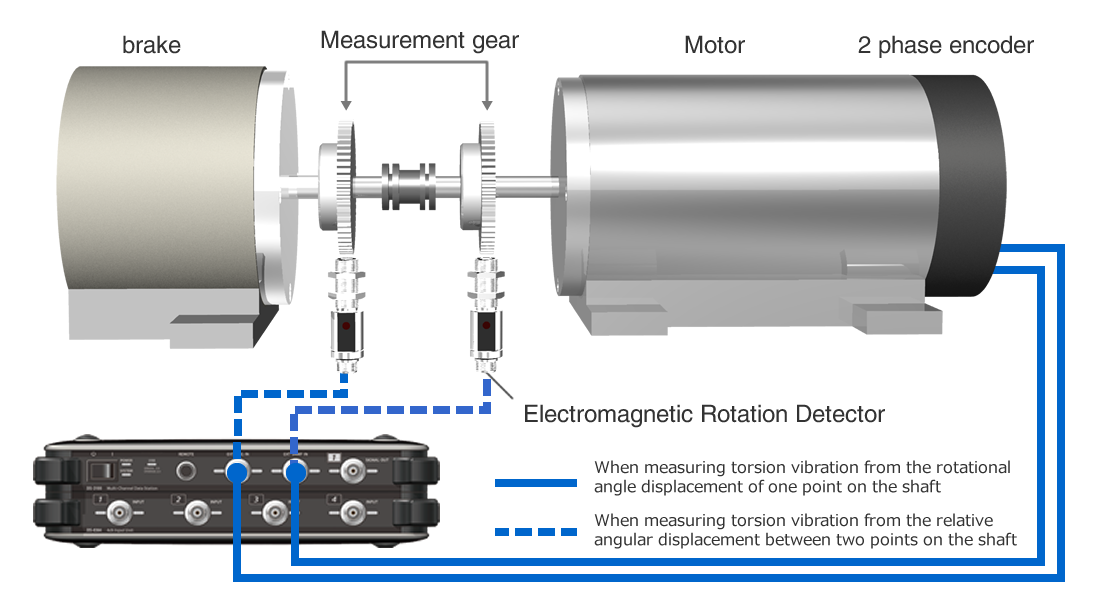
Application examples
Inspection of motor shaft torsion and rotation fluctuations
Torsion inspection of clutches and dampers
Rotation transmission measurement of drive unit, etc.
Example of system configuration
Specifications
Number of max.ch | 32 ch |
---|---|
Frequency analysis range | 40 kHz (2 to 8 ch)
20 kHz (10 to 16 ch) 10 kHz(18 to 32 ch) |
Number of analysis tracks | 16 tracks+OA |
Frequency analysis | FFT 6400 lines/bundled of octave |
Max. analysis order | 1600th order |
Rev. reference | Revolution1 / Revolution2 /calculation revolution of Rev.1 and Rev.2 |
Average | Exponential average/moving average |
Composite calculation | Sound : max.1ch, Vibration : max.10ch |
Front end | DS-3200series |
---|---|
OS | Microsoft Windows® 7 Ultimate/Professional SP1 (64-bit)
Microsoft Windows® 7 for Embedded Systems (64-bit) Microsoft Windows® 10 Pro, (64-bit) Microsoft Windows® 10 IoT enterprise 2019 LTSC Please refer to the software operating environment [Windows] for the details of the version. Microsoft .NET Framework 4.6 or later |
CPU | Equivalent to or faster than Intel Core TMi7 3 GHz |
Memory | 8GB or more |
Display | 800 X 600 or more |
Interface | USB 3.0 x 2 port or more or USB 3.0 x 1 port + USB 2.0 x 1 port or more |
Optical drive | CD/DVD drive (required in installation) |
Software·Option
Model name | Product name | Overview |
---|---|---|
GN-1100 | Noise Testing Software | Basic software, tracking and judgment of Rev 1 input, tracking analysis extension. |
GN-0100 | ORF Input & Recalculation Function | Reading ORF file, recalculation |
GN-0110 | Secondary Data Processing Function | Reading ORF file, recalculation, Campbell diagram, overlay function, rotation fluctuation (GN-0100 included) |
GN-0120 | GN Link Function | External communication function* of LAN (TCP/IP) |
GN-0130 | File Viewer Function | Search for data file, overlay, peak list display |
GN-0140 | Dual Rev Tracking Function | Simultaneous processing of tracking analysis and pass-fail judgment of 2 rotation inputs. |
GN-0150 | Calculation Rev Tracking Function | Simultaneous processing of tracking analysis and pass-fail judgment of three rotation inputs. |
GN-0160 | Dent Analysis Function | Dent judgment during tracking measurement of acceleration/deceleration |
GN-0170 | Real-time Octave Analysis Function
|
Pass/fail judgment by 1/3 octave analysis |
GN-0180 | Auto Sequence Function | Measurement function by command files (GN-0100 included) |
GN-0190 | Offset Tracking Function | Tracking analysis of the high frequency noise caused by inverter carrier signal. |
GN-0200 | Grade Line Function | Creating grade lines, setting of specification information, search function, output of peak data |
GN-0210 | Stress Tracking Analysis Function | Tracking of signal which requires DC calibration including a stress signal. |
GN-0220 | Torsion vibration operation function
![]() |
Calculating the torsional amount from the differences between two rotation speed signals (including GN-0140) |
GN-0230 | Envelop Analysis Function
![]() |
Abnormality detection judgment using envelope processing |
*
Windows®7 、Windows®10 are registered trademarks of Microsoft Corporation in the United States and other countries.
*
Intel, Intel logo, Intel Core, Core Inside are trademarks of Intel Corporation in the United States and other countries.
Related Information
Last update: 2022/4/8